Plate heat exchangers are widely used in various industries for efficient heat transfer between two fluids. They are known for their compact size, high thermal efficiency and ease of maintenance. When it comes to plate heat exchangers, the two common types are gasketed and welded plate heat exchangers. Understanding the differences between these two types is crucial to choosing the most appropriate option for a specific application.
Gasketed Plate Heat Exchanger:
Gasketed plate heat exchanger designs have a series of plates that are sealed together with gaskets. These gaskets create a tight seal between the plates, preventing the two fluids being exchanged from mixing. Gaskets are typically made from materials such as EPDM, nitrile rubber, or fluoroelastomer, depending on operating conditions and the fluid being handled.
One of the main advantages of gasketed plate heat exchangers is their flexibility. Gaskets can be easily replaced, allowing for quick maintenance and minimal downtime. Additionally, gasketed plate heat exchangers are suitable for applications where operating conditions may vary, as gaskets can be selected to withstand varying temperatures and pressures.
However, gasketed plate heat exchangers also have some limitations. Gaskets can degrade over time, especially when exposed to high temperatures, corrosive liquids, or frequent thermal cycles. This can lead to potential leaks and require more frequent maintenance.
In contrast, welded plate heat exchangers are constructed without gaskets. Instead, the plates are welded together to create a tight and permanent seal. This design eliminates the risk of gasket failure and potential leaks, making welded plate heat exchangers suitable for applications involving high temperatures, corrosive fluids, and high-pressure conditions.
The absence of gaskets also means that welded plate heat exchangers are more compact and have a lower risk of fouling because there are no gasket grooves in which deposits can accumulate. This makes them ideal for applications where space is limited and cleanliness is critical.
However, the lack of gaskets also means that welded plate heat exchangers are less flexible when it comes to maintenance and retrofits. Once the plates are welded together, they cannot be easily disassembled for cleaning or repair. Additionally, the initial cost of a welded plate heat exchanger is typically higher than a gasketed plate heat exchanger due to the precision welding required.
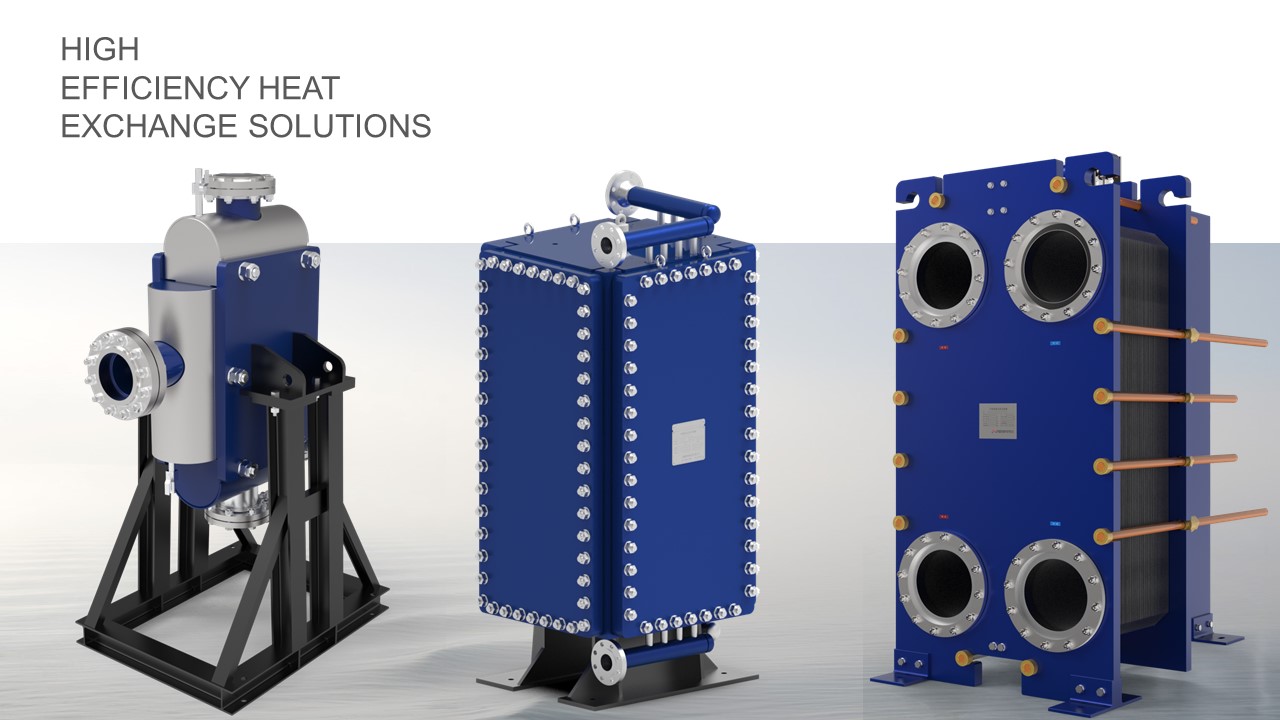
Main differences:
1. Maintenance: Gasketed plate heat exchangers are more convenient to maintain and flexible for modification, while welded plate heat exchangers have a more permanent and maintenance-free design.
2. Operating conditions: Gasketed plate heat exchangers are suitable for different operating conditions, while welded plate heat exchangers are more suitable for high temperature, high pressure and corrosive fluid applications.
3. Cost: The initial cost of a gasketed plate heat exchanger is usually lower, while the upfront investment of a welded plate heat exchanger may be higher.
In summary, the choice between gasketed plate heat exchangers and welded plate heat exchangers depends on the specific requirements of the application. Gasketed plate heat exchangers offer flexibility and ease of maintenance, while welded plate heat exchangers provide a stronger, longer-lasting solution for harsh operating conditions. Understanding the differences between these two types is crucial to choosing the most appropriate option for efficient and reliable heat transfer in a variety of industrial processes.
Post time: Aug-13-2024