Dans la production industrielle, les échangeurs de chaleur à plaques sont cruciaux pour transférer la chaleur et assurer des processus lisses. Ils transfèrent de l'énergie des fluides à haute température aux fluides à basse température, permettant une production efficace et efficace. Leur large applicabilité dans plusieurs industries souligne l'importance de choisir le bon environnement opérationnel pour maximiser l'efficacité de l'échangeur de chaleur, assurer la longévité et maintenir des performances optimales.
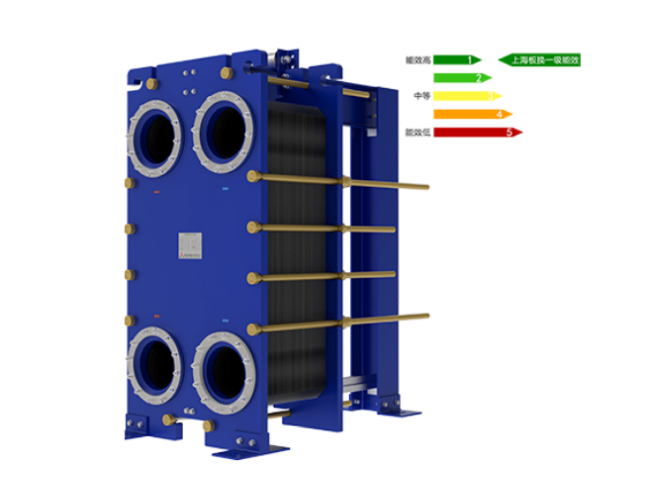
1. Caractéristiques moyennes
Avant de sélectionner unÉchangeur de chaleur assiette, il est essentiel d'analyser la composition chimique du milieu d'échange de chaleur pour détecter toutes les substances corrosives, telles que les acides (acide sulfurique, acide chlorhydrique), alcalis (hydroxyde de sodium) ou sels (chlorure de sodium). Par exemple, dans les usines chimiques, les liquides déchets peuvent contenir de faibles concentrations d'acide chlorhydrique (0,5% -1%) et de sels d'acide organique. Une analyse chimique approfondie aide à choisir le bon matériau, comme les plaques d'alliage de titane, pour résister à la corrosion.
Dans les industries comme la transformation des aliments, où la valeur du pH du milieu est presque neutre (par exemple, la production de yaourt), les plaques en acier inoxydable suffisent, assurant un transfert de chaleur optimal et une durée de vie plus longue. De plus, la détection d'impuretés dans le milieu, comme les particules solides, est cruciale pour prévenir le dépôt sur la surface de la plaque, ce qui pourrait diminuer l'efficacité.
2. Conditions de température
La mesure avec précision des températures d'entrée et de sortie du milieu d'échange de chaleur est essentielle. Dans les systèmes de chauffage, par exemple, la température de l'eau chaude peut varier de 100 ° C à 120 ° C et refroidir à 70 ° C à 80 ° C après échange de chaleur. La compréhension des fluctuations de la température est cruciale pour sélectionner un modèle d'échangeur de chaleur qui peut gérer des variations extrêmes sans compromettre l'intégrité structurelle.
3. Conditions de pression
Le maintien de la pression de travail de l'échangeur de chaleur dans la plage nominale est vital pour la sécurité. Par exemple, dans les raffineries de pétrole, où la pression du fluide peut atteindre jusqu'à 1,5 MPa, le choix d'un échangeur de chaleur évalué au-dessus de cette valeur garantit un fonctionnement sûr. La surveillance des fluctuations de la pression, en particulier dans les systèmes avec des pompes, est nécessaire pour éviter les dommages aux joints et assurer la stabilité.
4. Caractéristiques d'écoulement
Le débit a un impact direct sur l'efficacité de l'échange de chaleur et la chute de pression dans le système. Pour les petits systèmes, comme les unités de CVC commerciales, le débit peut être de quelques mètres cubes par heure, tandis que les plus grands systèmes industriels pourraient atteindre des milliers de mètres cubes par heure. La stabilité de l'écoulement garantit des performances d'échange de chaleur cohérentes.
5. Facteurs environnementaux externes
L'espace d'installation et les conditions environnementales environnantes comme la température, l'humidité et les sources de vibration doivent être prises en compte. Par exemple, dans des espaces serrés comme les salles de machines à navire, un modèle d'échangeur de chaleur compact est nécessaire pour s'adapter à l'environnement tout en laissant de la place à l'entretien.
Conclusion
En considérant les caractéristiques moyennes, les conditions de température et de pression, les propriétés d'écoulement et l'environnement d'installation, l'optimalÉchangeur de chaleur assiettePeut être sélectionné pour assurer une opération efficace et durable.
Heure du poste: sept-29-2024