En la producción industrial, los intercambiadores de calor de las placas son cruciales para transferir el calor y garantizar procesos suaves. Transfieren energía de fluidos de alta temperatura a fluidos de baja temperatura, lo que permite una producción eficiente y efectiva. Su amplia aplicabilidad en múltiples industrias subraya la importancia de elegir el entorno operativo adecuado para maximizar la eficiencia del intercambiador de calor, garantizar la longevidad y mantener un rendimiento óptimo.
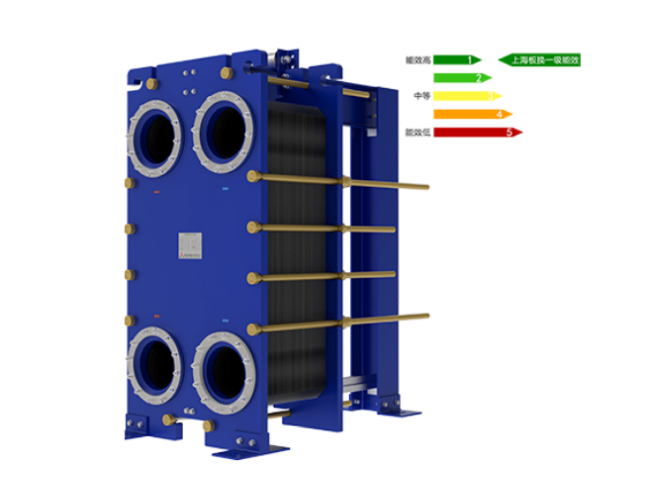
1. Características medianas
Antes de seleccionar unintercambiador de calor de placa, es vital analizar la composición química del medio de intercambio de calor para detectar cualquier sustancia corrosiva, como ácidos (ácido sulfúrico, ácido clorhídrico), álcalis (hidróxido de sodio) o sales (cloruro de sodio). Por ejemplo, en las plantas químicas, los líquidos de desechos pueden contener bajas concentraciones de ácido clorhídrico (0.5%-1%) y sales de ácido orgánico. Un análisis químico exhaustivo ayuda a elegir el material adecuado, como las placas de aleación de titanio, para resistir la corrosión.
En industrias como el procesamiento de alimentos, donde el valor de pH del medio es casi neutral (por ejemplo, producción de yogurt), las placas de acero inoxidable son suficientes, asegurando una transferencia de calor óptima y una vida útil más larga. Además, la detección de impurezas en el medio, como las partículas sólidas, es crucial para evitar la deposición en la superficie de la placa, lo que podría disminuir la eficiencia.
2. Condiciones de temperatura
Es esencial medir con precisión las temperaturas de entrada y salida del medio de intercambio de calor. En los sistemas de calentamiento, por ejemplo, la temperatura del agua caliente puede variar de 100 ° C a 120 ° C y enfriar a 70 ° C a 80 ° C después del intercambio de calor. Comprender las fluctuaciones de temperatura es crucial para seleccionar un modelo de intercambiador de calor que pueda manejar variaciones extremas sin comprometer la integridad estructural.
3. Condiciones de presión
Mantener la presión de trabajo del intercambiador de calor dentro del rango nominal es vital para la seguridad. Por ejemplo, en las refinerías de petróleo, donde la presión de fluido puede alcanzar hasta 1.5MPa, elegir un intercambiador de calor calificado por encima de este valor garantiza un funcionamiento seguro. El monitoreo de las fluctuaciones de presión, especialmente en sistemas con bombas, es necesaria para evitar daños a los sellos y garantizar la estabilidad.
4. Características de flujo
El caudal afecta directamente la eficiencia del intercambio de calor y la caída de presión en el sistema. Para sistemas más pequeños, como las unidades comerciales de HVAC, el flujo puede ser de unos pocos metros cúbicos por hora, mientras que los sistemas industriales más grandes podrían alcanzar miles de metros cúbicos por hora. La estabilidad en el flujo asegura un rendimiento constante del intercambio de calor.
5. Factores ambientales externos
Se debe considerar el espacio de instalación y las condiciones ambientales circundantes como la temperatura, la humedad y las fuentes de vibración. Por ejemplo, en espacios estrechos como salas de motor de barcos, es necesario un modelo compacto de intercambiador de calor para adaptarse al entorno mientras deja espacio para el mantenimiento.
Conclusión
Al considerar las características medianas, las condiciones de temperatura y presión, las propiedades de flujo y el entorno de instalación, el óptimointercambiador de calor de placaSe puede seleccionar para garantizar una operación eficiente y duradera.
Tiempo de publicación: septiembre-29-2024